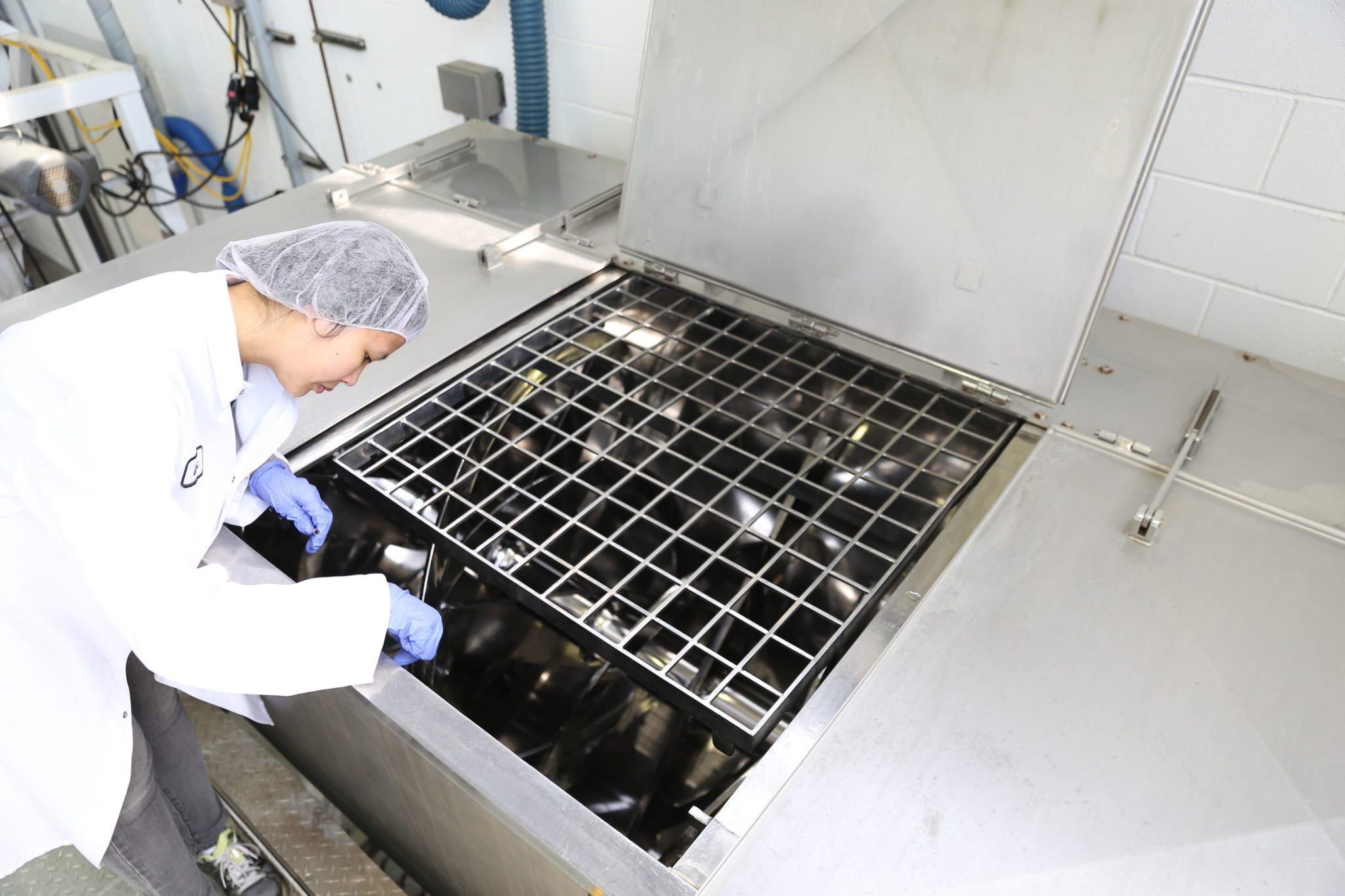
Swabbing
We utilize swabs on both food contact and non-food contact items in our facilities:
- Allergen swabbing is performed after products that have a US top-8 allergen have been run on food contact items
- ATP (Adenosine triphosphate) swabbing is done on both food contact and non-contact items to ensure a clean production environment for making products
- Environmental swabbing is done periodically in our facilities to confirm our plant’s overall cleanliness
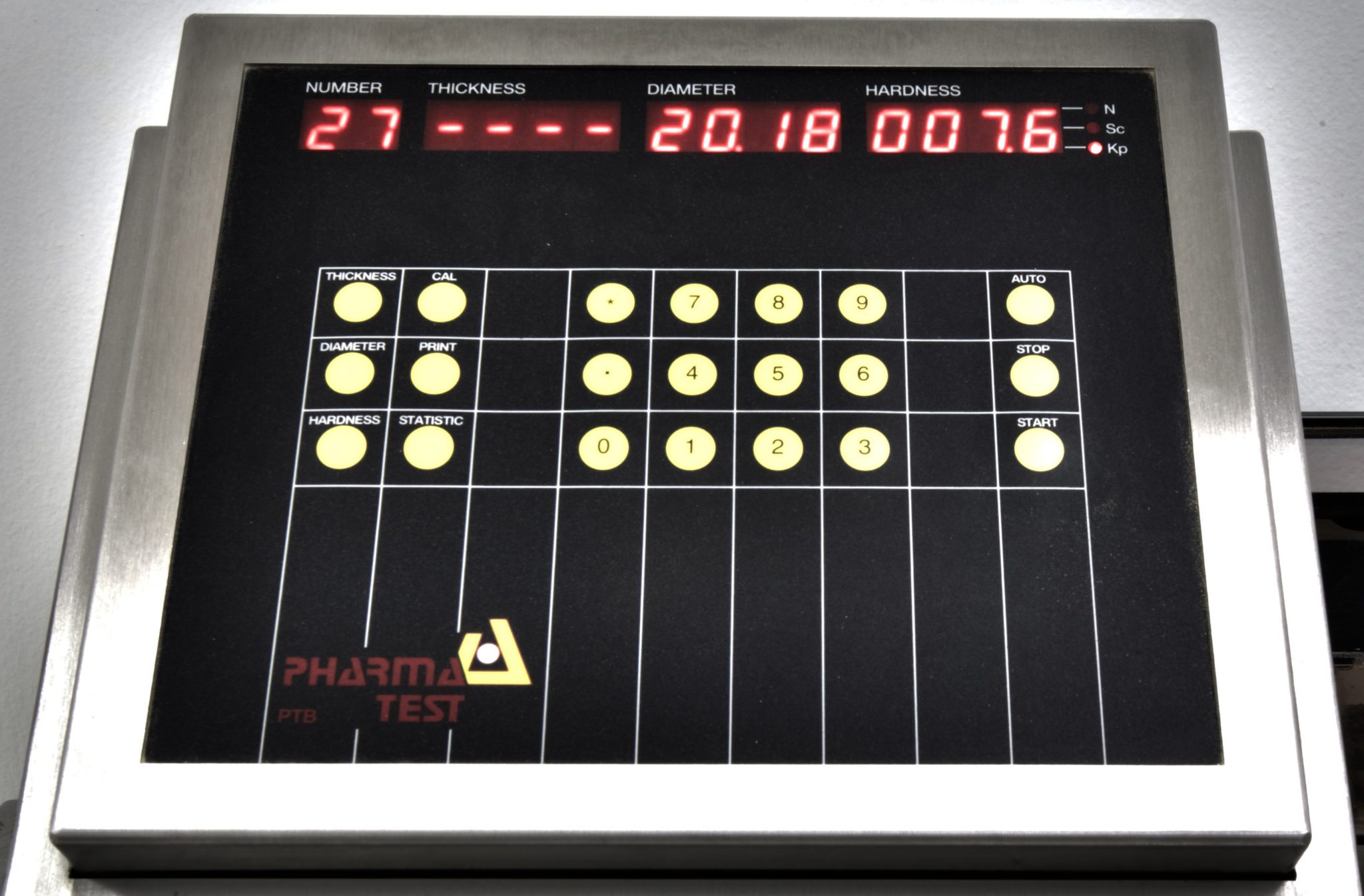
Tablet Hardness Testers
Our tablet hardness testers are used to determine the structural integrity of a particular tablet under conditions of storage, transportation, and handling before usage. We measure tablets in kp (kiloponds) which is equivalent to a kilogram of force.
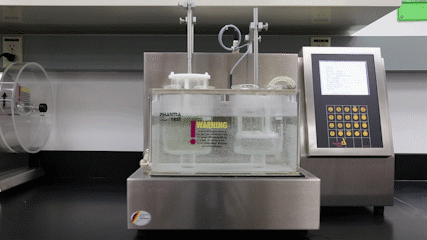
Tablet Disintegration Testers
USP Dissolution Apparatus 1 units are used in our lab to monitor disintegration times for tablets. It is important to properly replicate the same conditions when testing tablets, which is why we monitor the temperature and pH levels of the solution the tablets are being disintegrated in.
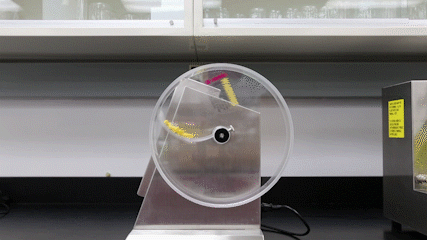
Tablet Friability Testers
Protein Research uses USP benchtop friability testers to analyze finished tablets’ tendency to chip, crumble or break once compressed. The test is done to replicate the transport and handling of tablets as well as their subsequent storage conditions.
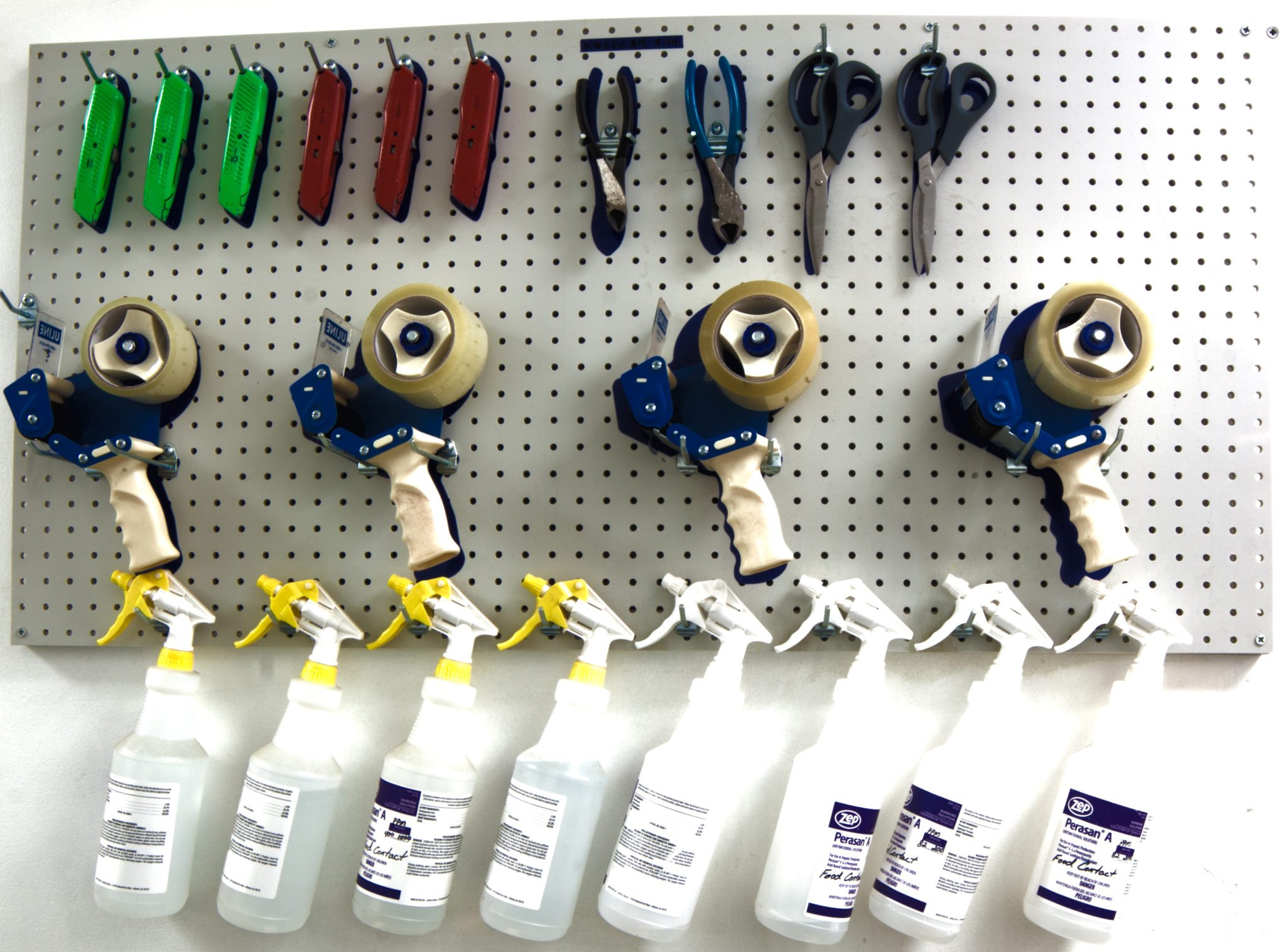
Shadow Boards
Shadow boards are used as a visual management tool with painted images of where specific production tools belong and show when tools are missing.
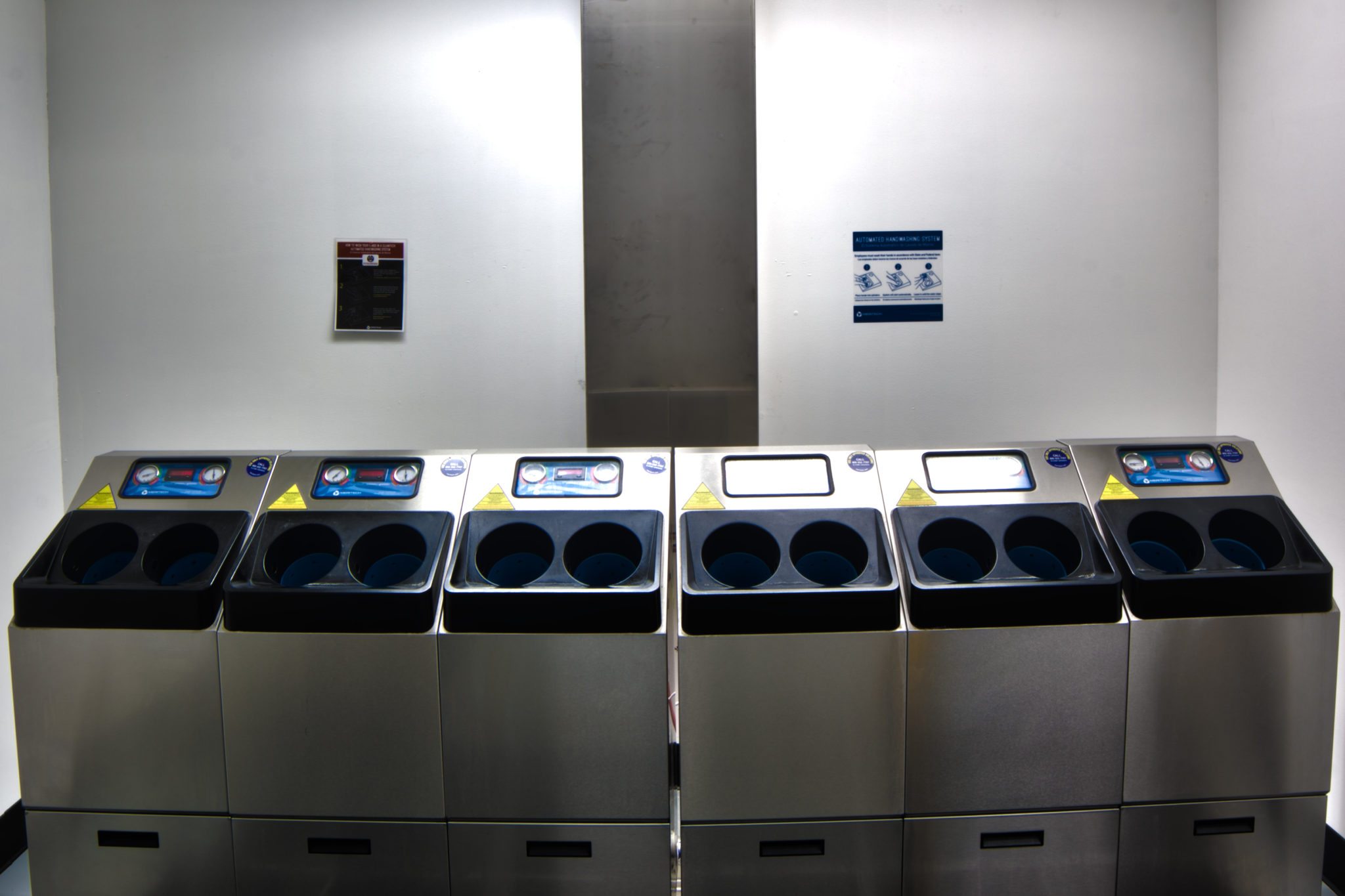
Hand/Foot Washing Station
HACCP and SSOP compliant hand/foot washing stations are in place at the entry point to the production area. Our state of the art automated machines exceed food safety standards for SQF and BRC. These machines give an automated hand wash and foot bath to each user before the individual is allowed access to the production area.
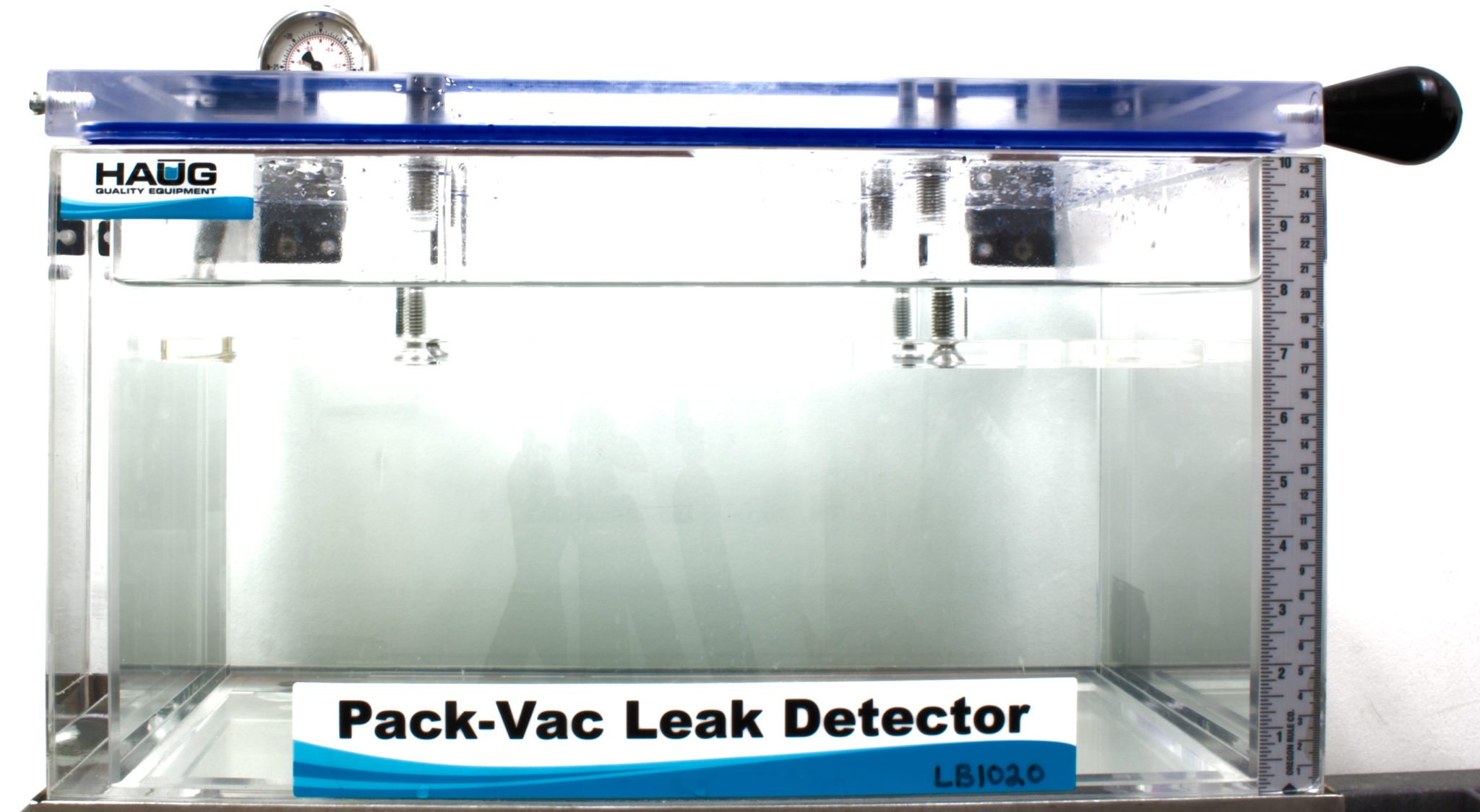
Leak Detecors
These devices help us ensure the seal integrity of our flexible packaging (stick packs, sachets, gusseted bags, etc.) to our clients before being boxed up and shipped out. Our devices utilize ASTM D3078 Standard Test Method.